Industrial > Abrasive, Sandblasting and Soda Blasting
What makes powder coating the best choice?
Powder coating looks like paint but acts like armor. It’s tough, attractive, cost-effective and easy on the environment. Powder coated products have established a technologically superior reputation for performance and durability.
How are products powder coated?
Finely ground particles of pigment and resin are electrostatically charged and sprayed onto the surface to be coated. The charged powder particles adhere to the electrically grounded surfaces until the powder is heated and fused into a smooth coating in the curing oven. The result is a uniform, durable, high quality finish.
Powder coating is one of the most economical, longest lasting, and most color-durable quality finishes available for metal. Powder coated surfaces are more resistant to chipping, scratching, fading and wearing than other finishes. You can choose from smooth to textured finishes....and colors from flat to semi-gloss to high gloss.
SANDBLASTING: A quality finish starts with the proper surface preparation. We have our own in-house sandblasting booth. Sandblasting our own items allows us be in control of the entire powder coating process from start to finish. Our large blast room lets us handle both large and small jobs with ease.
CLEANING PROCESS: We hand clean all items to ensure proper adhesion. Our pre-treatment process has been proven successful on steel, aluminum and galvanized substrates. Products pass through our oven prior to the application of powder to "bake-off" any oils or grease that may still be on or inside the part.
PREPARATION: High temperature masking tape is applied to designated surfaces to keep them from being coated. Silicon plugs and caps are used for threaded holes or shafts to protect them. The oven temperature makes the use of plastic and resin body fillers hard to use. Often the powder will not bind to a filler's surface, leaving it exposed.
POWDER COATING: Our oven and Gema coating system ensures a superior finish for your item. The powder coating process uses a dry mix of plastic resins, pigments and fillers that melt and fuse together when heated. The powder is applied by an electrostatic charged spray gun and carried by low velocity air to the surface of the piece to be coated. The electrostatic charge holds the powder particles in place so that the charged particles adhere to them until melted and fused into a solid coating in the curing oven.
CURING OVEN: Once coated, the part is rolled into the curing oven and baked on. The heat of the oven causes a chemical reaction that melts the dry powder to a liquid and then the curing process causes it to harden, creating a highly durable finish.
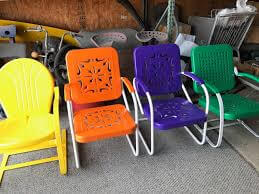
Details
- Last Updated
- 30/Jul/2025
- Contact
- Billy Meister
- [email protected]
- Phone
- (817) 759-2224
- Website
- http://www.longhornpowdercoating.com/
- Address
- 2516 Minnis DrHaltom City, TX 76117